Laserhärten
Kurz erklärt
Vorteile
- Sehr verzugsarm
- Schnell
- Berührungslos
- Keine Abschreckmittel notwendig
- Härten von genau definierten Bereichen möglich
- Härteverlauf definierbar
- Höchste Härtewerte erreichbar
Verfahren
- Martensitisches Umwandlungshärten
- Randschicht wird in Martensit umgewandelt
- Intensität und Einwirkdauer des Lasers muss auf Gefüge - Umwandlung abgestimmt sein
- Vorteil: schnelles aufheizen, wegfall der Haltezeit
- Schockhärten
- Oberfläche wird mit Laserpulsen bestrahlt
- Hoher Druck führt zu Stoßwellen, diese führen zu plastischer Verformung des Materials
- Anwendung bei Titan- und Aluminiumlegierungen in der Luft- und Raumfahrt
- Beschichten
- Zusätzlicher Werkstoff wird auf das Grundmaterial aufgeschlmolzen
- Schutz des Grundmaterials vor Korrosion und Verschleiß
- Umschmelzhärten
- Bildung feinerer und homogenerer Gefüge - Strukturen
- Durch die sehr hohe Abkühlrate kommt es zu einer sehr schnellen Erstarrung
Video
Videotext
Das Laserhärten fällt in den Bereich der Wärmebehandlung. In der Industrie werden heutzutage sehr viele Stähle wärmebehandelt, um die gewünschten Eigenschaften zu erhalten. Wärmebehandlungen werden in Glühen, Härten und Vergüten unterteilt. Das Härten wird weiter in Härten, bei dem das ganze Werkstück gehärtet wird, und Randschichthärten unterteilt. Beim Laserhärten handelt es sich um einen Randschichthärtevorgang. Der Härtevorgang ist beschränkt auf geringe Eindringtiefen an der Oberfläche des Werkstückes.
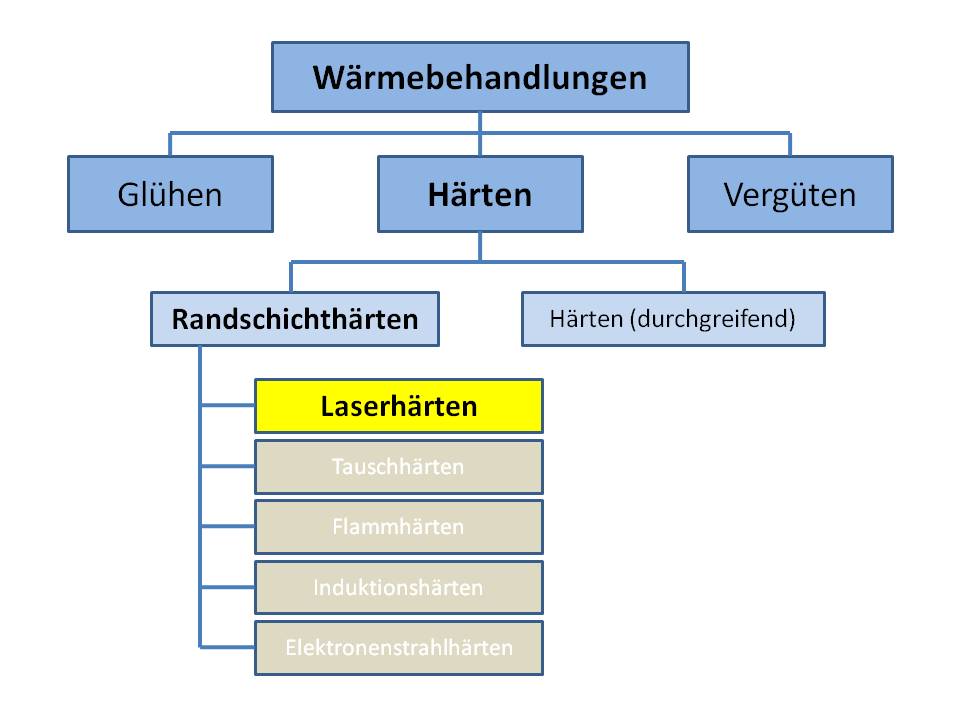
Das Laserhärten besitzt viele Vorteile. Die Härtung ist sehr verzugsarm, sie ist schnell und berührungslos und es sind keine Abschreckmittel notwendig. Ein weiterer wichtiger Vorteil liegt in der Möglichkeit, nur genau definierte Bereiche zu härten und der Möglichkeit den Härteverlauf an die Bauteilgeometrie anzupassen, sowie das Härten von schwer zugänglichen Bereichen. Durch das Laserhärten sind höchste Härtewerte erreichbar.
Das Laserhärten lässt sich in vier unterschiedliche Verfahren einteilen, die je nach Werkstoff derzeit im Einsatz sind. Dies sind das martensitische Umwandlungshärten, das Schockhärten, das Umschmelzen und das Beschichten.
Beim martensitischen Umwandlungshärten wird die Randschicht des Werkstückes in ein martensitisches Gefüge umgewandelt. Dies erfolgt durch eine Aufheizung durch den Laserstrahl und einer anschließenden Selbstabschreckung des Materials. Die Selbstabschreckung erfolgt durch den Wärmefluss im Material selbst. Wichtig ist, die Intensität und die Einwirkdauer des Lasers auf die benötigte Zeit zur Gefüge - Umwandlung anzupassen. Der Vorteil gegenüber einem herkömmlichen Härtevorgang ist die sehr schnelle Aufheizung des Werkstücks und der Wegfall des Haltens der Härtetemperatur durch höhere Temperaturen.
Beim Schockhärten wird die Oberfläche des Werkstoffes mit Laserpulsen bestrahlt. Dadurch baut sich in kurzer Zeit ein sehr hoher Druck auf. Dieser hohe Druck führt zu Stoßwellen, die sich ins Werkstückinnere ausbreiten wodurch es zu einer plastischen Verformung des Materials kommt. Diese Verformung führt nach Ende des Vorgangs zu bleibenden Druckspannungen im Material. Das Schockhärten wird bei Aluminium- und Titanlegierungen für die Luft- und Raumfahrt angewandt. Die entstehenden Spannungen haben eine positive Auswirkung auf das Ermüdungsverhalten des Materials.
Beim Beschichten wird ein zusätzlicher Werkstoff auf das Grundmaterial aufgeschmolzen. Der zusätzliche Werkstoff soll das Grundmaterial schützen und besitzt im Allgemeinen bessere Eigenschaften hinsichtlich Verschleiß und Korrosionseigenschaften. Zur Aufbringung des Materials wird es aufgeschmolzen und verbindet sich mit dem Grundmaterial.
Mit dem Umschmelzhärten bzw. Glasieren werden feinere und homogenere Gefüge - Strukturen im Vergleich zum Ausgangszustand erreicht. Dies wird durch eine sehr hohe Abkühlgeschwindigkeit der Schmelze erreicht, wodurch es zu einer sehr schnellen Erstarrung kommt. Durch das Umschmelzhärten kommt es zu einer Erhöhung der Härte, Zähigkeit und der Verschleiß- und Korrosionsbeständigkeit. Durch die sehr schnelle Abkühlung kann es zur Bildung einer glasartigen Schicht kommen, weshalb man auch vom Glasieren spricht.